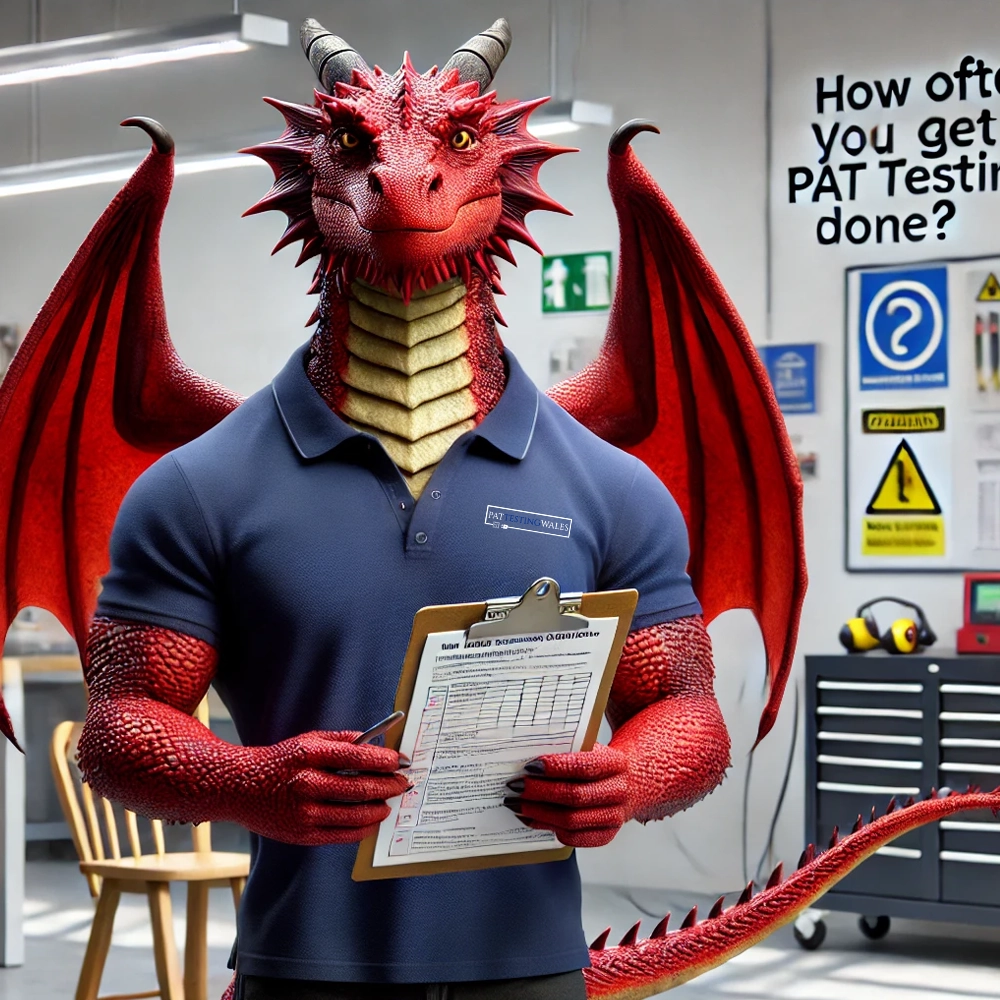
How Often Should You Get PAT Testing Done?
Portable Appliance Testing (PAT) is a vital part of maintaining electrical safety in the workplace. While there is no specific legal requirement for how often PAT testing should be conducted, employers are obligated under the Electricity at Work Regulations 1989 to ensure all electrical equipment is safe to use. Determining the appropriate frequency of PAT testing depends on various factors, including the type of equipment, its use, and the environment in which it operates.
At PAT Testing Wales, we specialise in helping businesses across Wales establish effective PAT testing schedules that prioritise safety and compliance. In this blog, weโll explore the factors influencing PAT testing frequency and provide practical recommendations tailored to different workplaces.
What is PAT Testing?
PAT testing involves the inspection and testing of electrical appliances to ensure they are safe to use. The process includes:
- Visual Inspection: Checking for visible damage such as frayed wires or cracked plugs.
- Electrical Testing: Using specialised equipment to test for internal faults like poor insulation or earth continuity issues.
- Labelling and Reporting: Appliances are labelled with pass/fail stickers, and detailed reports are provided for compliance purposes.
PAT Testing Wales ensures all testing is conducted to the highest standards, providing peace of mind and safety for your workplace.
Factors Influencing PAT Testing Frequency
The frequency of PAT testing is not a one-size-fits-all rule. Instead, it depends on several factors:
1. Type of Equipment
- Handheld Devices: Equipment such as power tools or kettles, which are moved and used frequently, are more prone to wear and tear.
- Stationary Equipment: Appliances like printers or desktop computers are less likely to sustain damage due to their fixed location.
2. Environment
- High-Risk Environments: Construction sites, workshops, or kitchens involve more demanding conditions, increasing the risk of damage to electrical appliances.
- Low-Risk Environments: Offices, retail spaces, and classrooms typically involve lower levels of risk.
3. Frequency of Use
- High-Usage Equipment: Devices used daily are more likely to develop faults.
- Occasionally Used Equipment: Items used infrequently may require less frequent testing but still need regular inspections.
4. Manufacturerโs Recommendations
Manufacturers often provide guidance on maintenance and inspection schedules for their equipment. Following these recommendations helps ensure safety and compliance.
5. Results of Previous Testing
- Appliances that frequently fail PAT tests may require more frequent checks.
- Equipment with a history of passing tests consistently may not need to be tested as often.
Recommended PAT Testing Frequencies
Although there are no strict legal timelines for PAT testing, the Health and Safety Executive (HSE) provides general guidelines based on the type of equipment and its environment:
Environment | Type of Equipment | Recommended Frequency |
Offices and Shops | Computers, printers, etc. | 2-4 years (visual checks annually) |
Offices and Shops | Portable items (kettles) | 1 year (or more frequently) |
Construction Sites | Handheld tools | Every 3 months |
Schools | IT equipment | 2-4 years |
Schools | Kitchen appliances | 1 year |
Industrial Settings | High-risk equipment | 6 months – 1 year |
Hotels and Hospitality | Guest room appliances | 1 year |
Note: These recommendations should be adapted to your specific business needs. At PAT Testing Wales, we provide tailored advice to help you determine the ideal testing schedule.
Visual Inspections vs. PAT Testing
While PAT testing involves electrical checks, regular visual inspections can also help identify faults early. Encourage employees to look for:
- Frayed or exposed wires.
- Burn marks around plugs or sockets.
- Loose or damaged components.
Visual checks should be performed more frequently than PAT testing and can be integrated into daily operations.
Legal and Insurance Considerations
Although PAT testing frequency is not set in law, maintaining a regular schedule is critical for:
- Compliance: Under the Electricity at Work Regulations 1989, employers must ensure electrical equipment is safe.
- Insurance Claims: Many insurers require proof of regular PAT testing in the event of a claim related to electrical faults.
How PAT Testing Wales Can Help
At PAT Testing Wales, we work with businesses of all sizes to establish effective PAT testing schedules. Our services include:
- Tailored Testing Plans: Based on your environment, equipment, and usage.
- Expert Testing: Certified technicians using advanced equipment to ensure safety and compliance.
- Detailed Reporting: Clear documentation to support legal and insurance requirements.
- Flexible Scheduling: Minimising disruption to your operations.
FAQs About PAT Testing Frequency
Do all appliances need PAT testing?
Not all appliances require formal PAT testing. Low-risk items such as desktop computers may only need visual inspections. However, high-risk or frequently used equipment should be tested regularly.
How do I know when my appliances were last tested?
Each appliance tested by PAT Testing Wales is labelled with the date of the last test and the recommended retest date. We also provide detailed reports for your records.
What happens if an appliance fails a PAT test?
Failed appliances should be removed from use immediately. PAT Testing Wales can advise on repair or replacement options to ensure compliance.
Final Thoughts
Determining how often PAT testing is required depends on a range of factors, including the type of equipment, its environment, and how often itโs used. Regular testing is essential for ensuring workplace safety, maintaining compliance, and protecting your business from risks associated with faulty electrical appliances.
If youโre unsure about the right PAT testing schedule for your business, contact PAT Testing Wales today. Our expert team will work with you to develop a testing plan tailored to your needs, ensuring your workplace remains safe and compliant. Together, we can keep your employees, customers, and business protected.